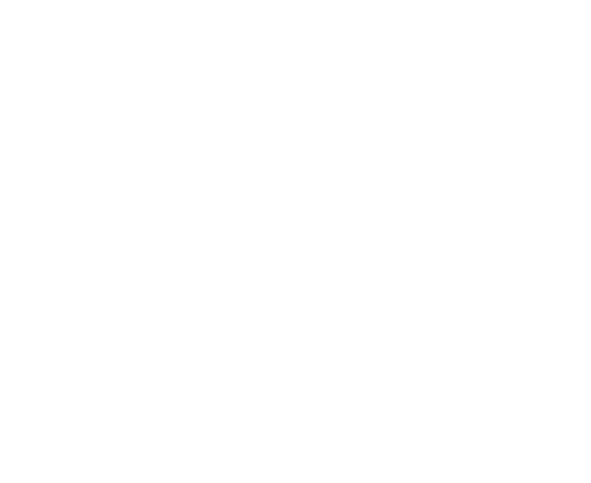
MEASUREMENTS
In order to save the architects' time and effort, all measurements of the furnishable office are done by our project manager. The process involves communication with builders, electricians, plumbers and other specialists in order to understand their plans for project implementation and how to fit them together.